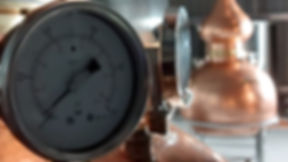

Toulvaddie is a brand new micro whisky distillery in Fearn the North East, Highlands of Scotland.
​
Watch the video below or click here to follow the progress.
Nobody said it would be easy to build a modern day whisky distillery and yes, it has been quite a journey, with many hurdles to overcome to get to here today.
​
Starting at the very beginning, we were very lucky to be gifted the land on which we have built the distillery by Bobbys parents, Ronnie and Maggie.
​
When I first applied for distillery planning, everything looked like it was all going to fall in to place nicely. Planning passed approval within 4 weeks stating it was an ideal use for the site. Hooray, you would think – there were some conditions attached to the planning approval, which I had expected, as its former use was as a Royal Naval Airbase, HMS Owl.
One of the conditions was to have soil sampling done. A Scientist from the Envirocentre completed a Phase 1 Site investigation and confirmed the land was fit for use and submitted their report to the council – who unfortunately disagreed with the findings and requested that a Phase 2 report be done. After 6 months the type of tests had been decided upon . Once again an Envirocentre scientist came out to carry out their survey and samples.They completed their second site inspection and produced a 54 page report, with the same outcome as the first and accepted by the council.


This was not the end of the delays, after 2 years a building warrant was finally granted. This allowed the construction phase to state
​
Having delays in getting permissions granted had a serious knock on effect with the timeline, Contractors who I had in line for completing the works now had other commitments, so I decided the only way to get things going was to do it myself.
From laying out the site, digging the pad holes, to building the shutters for the concrete, was an extremely steep learning curve, resulting in some very long days and nights in temperatures as low as -7°.


The very first pour of concrete was not only extremely nerve wracking as it is at this stage I would know if I have got my shuttering levels correct, but it was also the first time where I actually felt a bit of emotion creep up on me. Up until this point, it was all consuming. Constantly going through my head, Is the pad square? are the footing pads all at the same level? will the weather hold so that we can actually pour the concrete? The moment the first drop came off the ready mix lorry it really felt like major progress, finally out of the ground, such a great feeling and I am happy to report that the pads were all level, and the floor pad was square!




Unfortunately due to Brexit delays and shut downs, I had missed my construction time slot with the local steel erector for the distillery building. They now had a several month long waiting list due to projects being put on hold, and I did not have the time to spare. The building came with a self build guide, so that is what I decided to do.
​
Bolted together on the ground, with the help of family and friends, we erected the building, bay by bay. I have to say, the very first lift was probably one of the most stressful moments of the whole build. It does state in the self-build guide that it is designed to flex when lifted – however when you do not know the degree that it can flex, it is a very daunting moment. We aborted the first attempt to see if there was a better way. In the end we decided we would just go for it, and success! Once you are aware that flexing is normal, it is a less stressful process – not stress free, but it was one less thing to worry about.

The next step was putting on the roof. This was point where it would be evident if we put the structure up square or not. With a family friend and my dad up on the roof- and me, my husband and another friend on the ground, we managed to get the roof completed in a single day.

​
Now we were under cover, we could start work on the floor. Drains had to be in place before we could add the damp proof course, the reinforcement bars and then the concrete. After having dug the pad holes I did not relish the thought of breaking through more of this ground. Digging would always start off easy, but when you thought you hit a small stone, you would often find it was actually a large boulder, which always happened to be in the line of the drain! Luckily, my mother was up for giving it a go and was very adept at swinging a pick and digging out several metres worth of underground drains.

The first ready mix lorry turned up at 7.30am to pour the first bay. Pouring a concrete floor is not the same as pouring the pads. It was certainly a workout moving the concrete with a concrete rake! In each bay, the same thing happened. The day would start out clear, blue skies, but as we would finish the pour, the heavens would open and we were combatting torrential rain. Rain and concrete do not go well together and my husband would spend hours after the concrete was poured with a float to smooth off the finish. He did a fantastic job. When it came to the last bay, the weather really turned quick. He was doing everything he could to stop the rain from ruining the floor surface. My parents turned up with tarpaulins and they tried to stop as much of the rain as possible, and then picked up the small edging floats and got stuck in too.


Stripping off all the shuttering once the floor had cured was one of those moments where the emotion creeps up on you again. It wasn’t always at the times that you thought it would hit you that you were getting somewhere, but knowing how much time I had put in to making the shuttering, the removal of it was confirmation that I had got it right, that we were making progress.

Fearn aerodrome is a very windy place. We have numerous windmills around in various sizes, which meant that when it came to putting up the metal sheeting for the walls this was done very carefully, and between gusts. My dad was up on the scaffolding and my mum and I would stand the sheet up before fixing in place. Most sheets were only 4.2m long, which is long enough when a gust of wind comes, but the longest ones were 5.3 meters. That may not sound like a big difference, but believe me, it is!
​We started with the back wall as that was the easiest, no cuts, no changes in height. It went up in no time. The other three walls have doors and the gable walls are peaked so they were a little trickier.


To skip back a little, when the main frame was going up it appeared to me that we had an upright beam missing. I triple checked the build list and we had everything it said we should. However when it came installing the cladding and the roller door on the front gable wall it was evident that it was missing. I contacted the company and sent them pictures and they agreed, there should be another upright! This meant waiting for the beam to come from Carlisle.
This slowed progress down a little, but we could continue with the cladding around the other roller door. There were no instructions on how to do this part – at all. I just could not work out how these three pieces of trim all fitted together. I sent photographs to the supplier, who couldn’t help, and ones to my friend who had been helping with the build, but I got no response. Several hours later, and Youtube videos later (which didn’t help) I had the proverbial Eureka moment, when it just became obvious how to do it, and…how did I not see it before! I messaged my friend back saying that it was ok, I had worked it out. He messaged straight back saying he didn’t bother replying as he didn’t know and knew I would work it out! Thanks! He did however come and install the roller doors and our building is now wind and watertight.
Before the second roller door went in the mash tun, HLT and fermentation vessels were moved into the building as some of them were too tall to make it through the doors.
Because there was now equipment in the building, the painting of the floor had to be done over 4 days so that it could all be moved around.

The stills have been a long time in the making, and I was delighted when I was told that they were on their way and I should be expecting them 9 days later. Fantastic! Or so I thought. The ship in which they were coming on was delayed. This ship they were being transferred to was delayed. When they were finally in Greenock, they were delayed on the ship. I was told that they had cleared all the customs and were just waiting for the ship to dock and be unloaded and they would be on their way up. I got a delivery notice from the shipping company stating they would be there in 2 days time. So I asked the neighbouring farmer if I could use his telehandler as more than one forklift was required to unload. He said yes, and just to call when needed. The delivery date came, and the gate was being watched in anticipation – no lorry. The company apologised, and rebooked for the next week as that was the soonest they could deliver. The same thing happened again.

Rebooked again and third time lucky, the stills were on their way up the road. My brother works for the neighbouring farmer and had rearranged his working day around our delivery slot to ensure that the telehandler was free. However, the lorry turned up 6 hours early. So a quick call to the farmer who sent over one of his other workers in the telehandler as my brother was 25 miles away in a tractor.
It all worked out well in the end, and the stills and heating unit arrived safely.



With the stills built up and connected together its on to plumbing in the condensers.


The condensors did not take long to plumb in and our toilet facilities were done at the same time. I cannot tell you how good it felt to have a proper flushing toilet on site rather than a portaloo!
​
There are some things that you do not attempt yourself and we are lucky that one of of neighbours in the aerodrome is Sangster Electrical who have done our electrical installation for us.

.jpeg)

After a long wait for them to arrive, and then waiting for the weather to be in our favour, we finally got to top off the build with our roof vents. These along with our wall louvres will ensure the movement of fresh air through the building during distillation without the need for any use of extra energy.
![XIWS5119[1].JPG](https://static.wixstatic.com/media/21faa1_c76014e60df64ce696ab4fd54cdf3804~mv2.jpg/v1/crop/x_0,y_0,w_1588,h_1125/fill/w_250,h_175,al_c,q_80,usm_0.66_1.00_0.01,enc_avif,quality_auto/XIWS5119%5B1%5D_JPG.jpg)

![IMG_3055[1].JPG](https://static.wixstatic.com/media/21faa1_413c26685a2a4244a69ed4effbdaf015~mv2.jpg/v1/crop/x_0,y_143,w_3547,h_2368/fill/w_266,h_175,al_c,q_80,usm_0.66_1.00_0.01,enc_avif,quality_auto/IMG_3055%5B1%5D_JPG.jpg)
It has been a long and tough journey, but the best way to succeed is to keep going, and we did just that!
We are now a fully licenced distillery.

The tasting bar is now complete and ready for you all to come visit!

